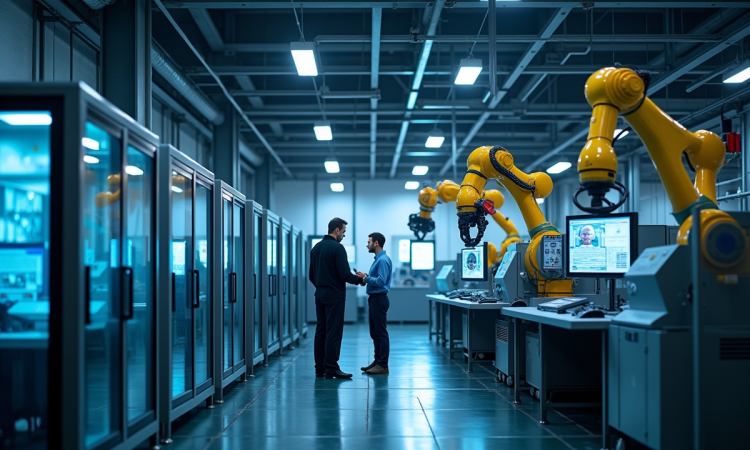
Les industries modernes se transforment à une vitesse fulgurante grâce aux avancées technologiques. Dans cet environnement en constante évolution, le choix entre numérique et analogique devient fondamental. Les capteurs numériques offrent une précision et une rapidité de traitement des données inégalées, permettant une meilleure gestion des ressources et une optimisation des processus de production.
Les technologies analogiques conservent leur pertinence, notamment dans des applications où la robustesse et la simplicité d’utilisation sont primordiales. Des secteurs tels que l’énergie ou la fabrication de produits de base continuent de s’appuyer sur des systèmes analogiques éprouvés pour leur fiabilité. Le débat est donc loin d’être tranché, chaque technologie ayant des atouts spécifiques selon les besoins de l’industrie.
Lire également : Les clés essentielles pour une formation en ligne réussie
Plan de l'article
Comprendre les différences entre technologies numériques et analogiques
L’Industrie 4.0 repose largement sur les technologies numériques pour optimiser les systèmes de production. Cela inclut l’utilisation de l’Internet des objets (IoT), de l’IIoT (Industrial Internet of Things) et de l’Edge Computing. Ces technologies permettent une collecte et une analyse de données en temps réel, facilitant ainsi la prise de décision et l’amélioration continue des processus industriels.
Technologies numériques
Les technologies numériques impliquent l’intégration de divers éléments :
A lire également : Améliorez les compétences de vos employés grâce à une formation interne efficace
- Objets connectés : Utilisés pour surveiller et contrôler les équipements de production.
- Réalité augmentée et réalité virtuelle : Employées pour former les employés et simuler des environnements de production complexes.
- Intelligence artificielle (AI) et Big Data Analytic : Utilisées pour analyser de grandes quantités de données et optimiser les opérations.
- Wi-Fi, Ethernet, LTE, et WAN : Fournissent les infrastructures de communication nécessaires pour connecter les systèmes et les dispositifs.
- Cloud computing : Plateformes comme Microsoft Azure et Amazon Web Service (AWS) sont utilisées pour stocker et traiter les données à grande échelle.
Technologies analogiques
Les technologies analogiques, bien que moins sophistiquées, conservent leur utilité dans certaines applications industrielles. Elles se caractérisent par leur robustesse et leur simplicité. Les secteurs comme l’énergie et la fabrication de produits de base continuent de les utiliser pour leur fiabilité éprouvée.
Industrie manufacturière et ligne de production bénéficient encore de ces technologies pour des tâches spécifiques où la précision numérique n’est pas nécessaire. Dans ce contexte, la transition entre les systèmes analogiques et numériques doit être soigneusement planifiée pour garantir une intégration harmonieuse et éviter des interruptions de production.
Les entreprises industrielles doivent donc évaluer leurs besoins spécifiques et la pertinence des différentes technologies pour réussir leur transformation numérique et maintenir une compétitivité accrue.
Les avantages des technologies numériques pour l’industrie 4.0
L’industrie 4.0 intègre diverses technologies numériques avec des avantages significatifs pour les systèmes de production.
Optimisation et flexibilité
L’utilisation de l’impression 3D et de la fabrication additive permet de produire des pièces complexes avec une grande précision. Ce procédé réduit les coûts et le temps de production tout en améliorant la flexibilité. Les cobots, ou robots collaboratifs, optimisent les tâches manuelles tout en garantissant la sécurité des opérateurs.
Amélioration des processus
Les technologies de simulation et de jumeau numérique permettent de tester et d’optimiser les processus avant leur mise en œuvre réelle. Les entreprises comme Siemens, Maya HTT et Simwell proposent des solutions pour modéliser et analyser les systèmes de production, réduisant ainsi les risques et les coûts.
Analyse et prise de décision
Les systèmes d’IIoT et d’Edge Computing collectent des données en temps réel, permettant une surveillance continue et une prise de décision rapide. L’analyse des Big Data améliore la qualité des produits et l’efficacité des opérations.
Cybersécurité et cloud computing
L’Industrie 4.0 implique la cybersécurité pour protéger les données sensibles. Le cloud computing, avec des plateformes comme Microsoft Azure et Amazon Web Service (AWS), facilite la mise à l’échelle des projets et l’accès aux ressources informatiques nécessaires.
Ces technologies numériques transforment les industries en offrant une flexibilité accrue, une meilleure qualité et une efficacité opérationnelle sans précédent.
Les applications des technologies analogiques dans l’industrie moderne
Les technologies analogiques continuent de jouer un rôle fondamental dans l’industrie moderne. Leur robustesse et leur fiabilité les rendent irremplaçables dans de nombreux contextes.
Fiabilité et robustesse
Les systèmes analogiques se distinguent par leur capacité à fonctionner dans des environnements extrêmes où les technologies numériques peuvent échouer. Ils sont souvent utilisés dans les secteurs pétrolier et gazier, où les conditions extrêmes requièrent une technologie éprouvée.
Applications spécifiques
Les technologies analogiques trouvent leur place dans les applications de sécurité où une défaillance n’est pas envisageable. Par exemple, dans les systèmes de contrôle des centrales nucléaires, les technologies analogiques offrent une redondance essentielle. Les systèmes analogiques sont utilisés dans les instruments de mesure de haute précision, tels que les oscilloscopes et les voltmètres.
Compatibilité et intégration
Les technologies analogiques sont souvent intégrées dans des systèmes hybrides, combinant le meilleur des deux mondes. Par exemple, les capteurs analogiques sont couramment utilisés avec des systèmes de contrôle numériques pour améliorer la précision et la fiabilité. Cette intégration permet une transition en douceur vers l’Industrie 4.0 tout en préservant les avantages des technologies analogiques.
- Robustesse dans des conditions extrêmes
- Redondance dans les systèmes de sécurité
- Compatibilité avec les systèmes numériques
Les applications des technologies analogiques dans l’industrie moderne montrent leur pertinence malgré l’essor des technologies numériques. Leur intégration dans des systèmes hybrides permet de bénéficier de la robustesse des technologies analogiques tout en profitant des avancées numériques.
Choisir la bonne technologie pour une transition réussie vers l’industrie 4.0
Comprendre les différences entre technologies numériques et analogiques
La transition vers l’industrie 4.0 implique une intégration poussée des technologies numériques. Ces technologies permettent d’optimiser les systèmes de production grâce à des objets connectés, la réalité augmentée et l’IIoT (Internet industriel des objets). Les technologies comme l’Edge Computing, l’AI (intelligence artificielle) et le Big Data Analytic sont désormais courantes dans les lignes de production modernes. Le Wi-Fi, l’Ethernet, le LTE et le WAN assurent la connectivité essentielle pour ces applications.
Les avantages des technologies numériques pour l’industrie 4.0
Les technologies numériques offrent de nombreux avantages. La réalité augmentée, par exemple, permet de superposer des données virtuelles sur la réalité, améliorant ainsi le contrôle et la maintenance des systèmes. L’impression 3D et la fabrication additive permettent de produire des pièces complexes avec une grande précision. Les systèmes de robotisation collaborative, comme les cobots, rendent les lignes de production plus flexibles et efficientes. Le cloud computing, via des plateformes comme Microsoft Azure et Amazon Web Service (AWS), accélère la mise à l’échelle des projets et assure une cybersécurité robuste.
Transition vers l’industrie 5.0
L’industrie 4.0 évolue déjà vers l’industrie 5.0, où l’humain est au centre de la transformation numérique. Jean-Philippe Raiche de Proaction International et François Blackburn-Grenon de Digifab QG mentionnent l’importance de l’intelligence industrielle pour cette nouvelle ère. Des entreprises comme Konnek et Worximity se positionnent en pionniers en intégrant des solutions avancées qui placent l’humain au cœur du processus de production.